Diffusionsschweißen
Diffusionsschweißen setzt eine erhöhte Diffusionsrate voraus. Da die Diffusionsgeschwindigkeit mit zunehmender Temperatur exponentiell zunimmt, wird typischer Weise die Fügetemperatur bei ca. 80% der Schmelztemperatur, berechnet in Kelvin, eingestellt.
Das Diffusionsschweißen wird in der Literatur in mehrere Phasen unterteilt (Abb. 1):
- Kontaktbildung durch Aufeinanderpressen zweier OF an Rauheitsspitzen
- Deformation der Rauheitsspitzen
- Diffusion über Korngrenzen, Korngrenzenwanderung
- Volumendiffusion zum Schließen der restlichen Porenräume
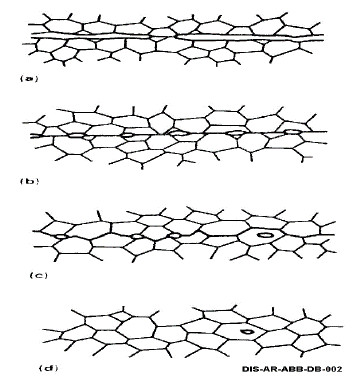
Der Fügeprozess muss je nach Material und zulässiger Verformung optimiert werden. Abhängig von Fügetemperatur und –druck ergeben sich verschiedene Fließraten, die auch zeitabhängig sein können. Für mikroverfahrenstechnische Bauteile liegt die optimale Verformung im Bereich von 3-5% der Bauteilhöhe. Im Idealfall sind die ehemaligen Fügeebenen nicht mehr sichtbar. Die mechanischen Eigenschaften diffusionsgeschweißter Bauteile wie Streckgrenze, Zugfestigkeit und Bruchdehnung erreichen werkstoffspezifische Werte. Allerdings geht Kaltverfestigung aufgrund von Rekristallisation verloren.
Als Diffusionsschweißöfen werden oft speziell umgebaute Zugprüfmaschinen verwendet. Aufgrund des starren Aufbaus können nicht nur Zug- sondern auch Druckkräfte gut übertragen werden. Der Werkstückraum mit Druckplatten zur Kraftaufbringung wird wie bei Zeitstandversuchsständen mit einem Ofen umgeben. Als Besonderheit kann dieser unter Hochvakuum betrieben werden. Damit wird die Oxidation von Metallen verhindert und Diffusion sichergestellt. Alternativ kann unter einer Schutzgasatmosphäre geschweißt werden.
Passivschichten können das Diffusionsschweißen erschweren. Während sich die Passivschicht z. B. auf Titan sehr gut im Metall löst, ist die Passivschicht auf Aluminium sehr stabil. Aluminiumwerkstoffe können entweder nur mit hohen Verformungen, die ein lokales Aufreißen der Passivschicht bewirken oder nach Entfernung der Passivschicht und Aufbringen einer oxidationsunempfindlichen Zwischenschicht, die eine niedrige Liquidustemperatur aufweist, diffusionsgeschweißt werden.
Auch für Edelstähle und Nickelbasislegierungen unterscheiden sich die Passivschichten je nach Legierungszusammensetzung.
Typischer Weise sind mikroverfahrenstechnische Apparate aus einer Vielzahl dünner, mikrostrukturierter Blechlagen aufgebaut. Daher wird das Diffusionsschweißen am IMVT genutzt, um über den gesamten Bauteilquerschnitt einfach vollflächige Verbindungen zu erzeugten. Im Ergebnis entstehen Apparate mit hervorragender Hochdruckfestigkeit.
Je nach Kanalgeometrie und effektiver Fügefläche bezogen auf die Gesamtfläche entstehen Fügeparameterabweichungen im Vergleich zu den an massiven Proben bestimmten Werten. Grund sind Abstützungseffekte. Die effektive Fügefläche sollte in allen Lagen ähnlich sein. Gegebenenfalls sollten funktionslose Hilfsstrukturen für ein optimales Fügeergebnis vorgesehen werden.
Das Institut verfügt über drei Diffusionsschweißöfen, deren maximale Fügekraft sich jeweils um den Faktor zehn unterscheidet (Abb. 2 bis Abb. 4). Dies widerspiegelt die historische Entwicklung der Mikroverfahrenstechnik, die immer anspruchsvollere und großformatigere Bauteile für industrielle Anwendungen mit entsprechenden Durchsätzen erforderlich machte.
[1] M. W. Mahoney, C. C. Bampton (Ed.): “Fundamentals of Diffusion Bonding”, Welding, Brazing and Soldering ASM Handbook. Vol. 6, ASM, S. 156-159, 1995
zurück