Versuche mit Keramikpulver
Keramische Werkstoffe zeichnen sich durch hohe Festigkeit und Härte, Temperaturstabilität, Verschleiß- und Korrosionsbeständigkeit aus. Diese spezifischen Werkstoffeigenschaften von Keramiken erfordern eine werkstoff- und fertigungsgerechte Konstruktion. Die konstruktiven Freiheiten werden jedoch besonders bei der Fertigung über Abformtechniken und Sintern stark eingeschränkt. [1]
Zur Fertigung kleiner Bauteile oder Systemkomponenten für die Mikroverfahrenstechnik aus Keramik, die nicht durch Abformtechniken herstellbar sind, erscheint die SLM-Technik als ein neues interessantes Fertigungsverfahren um auch Keramikpulver als Ausgangswerkstoff zu nutzen.
Der erfolgreiche Einsatz von Keramikpulvern im SLM-Prozess setzt voraus, das es grundsätzlich möglich ist die Pulverkörner in der Pulverschicht so zu verdichten bzw. aufzuschmelzen, daß rissfreie und dichte Strukturen (Bauteile) herzustellen sind.
Im SLM-Prozess werden pulverförmige Werkstoffe ganz oder zumindest teilweise aufgeschmolzen. Dabei entstehen extreme Temperaturgradienten im Schmelzbereich. Unter dieser Randbedingung erscheint der erfolgreiche Einsatz von Keramikpulvern eher unrealistisch.
Die Tatsache, dass beim Thermischen Spritzen aufgeschmolzene Keramikpulverpartikel in Form kleiner Schmelztropfen auf eine Oberfläche "gesprüht" werden und so mehre cm dicke feste Schichten herzustellen sind, begründet die Frage ob auch im SLM-Prozess Keramikpulver zu einer festen Struktur verdichtet werden kann. In beiden Verfahren wird das Pulverkorn sehr schnell aufgeschmolzen und wieder abgekühlt.
Zum thermischen Spritzen werden eine Vielzahl von Keramikpulvern bzw. Pulverrezepturen industriell angeboten. Für die Versuche auf der IMVT SLM-Anlage wurde folgende Oxidkeramik ausgewählt:
Al2O3/TiO2 97/3 (AMPERIT® 742 / Hersteller: H.C. Starck GmbH)
Al2O3/TiO2 97/3 (IKH 2001 / Hersteller: Industriekeramik Hochrhein GmbH)
Pulverzusammensetzung: 97% Al2O3 + 3% TiO2
Pulverkörnung: -25 +5 µm
Die SLM-Prozessparameter wurden in folgendem Parameterfeld variiert:
Laserleistung: | PLaser = 15 .. 25 W |
Bahngeschwindigkeit: | vBahn = 0,05 .. 1 m/s |
Laserspot: | DSpot = 25 .. 50 µm |
Pulverschichthöhe: | HSchicht = 30 .. 50 µm |
Vorheiztemperatur: | ϑ = 150 .. 250 °C |
Die ersten Versuche mit einer Einfachbelichtung brachten keine zufriedenstellenden Ergebnisse. Die Pulverschicht konnte nur teilweise aufgeschmolzen werden. Eine Ergebnisverbesserung war nur durch eine verbesserte Belichtungsstrategie zu erwarten. Die Idee war, den Energieeintrag zum Aufschmelzen der Pulverschicht auf mehrere Belichtungsschritte zu verteilen (Mehrfachbelichtung). Die Belichtungszeit pro Schritt wird dadurch verkürzt. Durch die Pausen zwischen den Belichtungsschritten hat das System Pulver-Schmelze mehr Zeit zum Temperaturausgleich und zur Materialbewegung im Schmelzbereich. Um die Mehrfachbelichtung zu realisieren wird der Vorwärtsbewegung des Laserstrahls eine Rückwärts- und Seitwärtsbewegung überlagert. Der Energieeintrag im Schmelzbereich kann so gezielt orts- und zeitabhängig variiert werden.
Mit dieser Mehrfachbelichtungsstrategie konnte das Keramikpulver sicher aufgeschmolzen werden. Abb. 1 zeigt zum Beispiel ein 1,5 mm hohes Rohrsegment mit einem Durchmesser von 4 mm, die Wandstärke beträgt etwa 300 µm. Als Träger wurde eine gesinterte Al2O3 Platte verwendet. Mit den gewählten Prozessparametern konnte das Rohrsegment problemlos aus 30 µm hohen Schichten auf der Trägerplatte aufgebaut werden. In der Rohrwand findet man aber noch Risse die zum Teil auch senkrecht von unten nach oben verlaufen (Abb. 2).
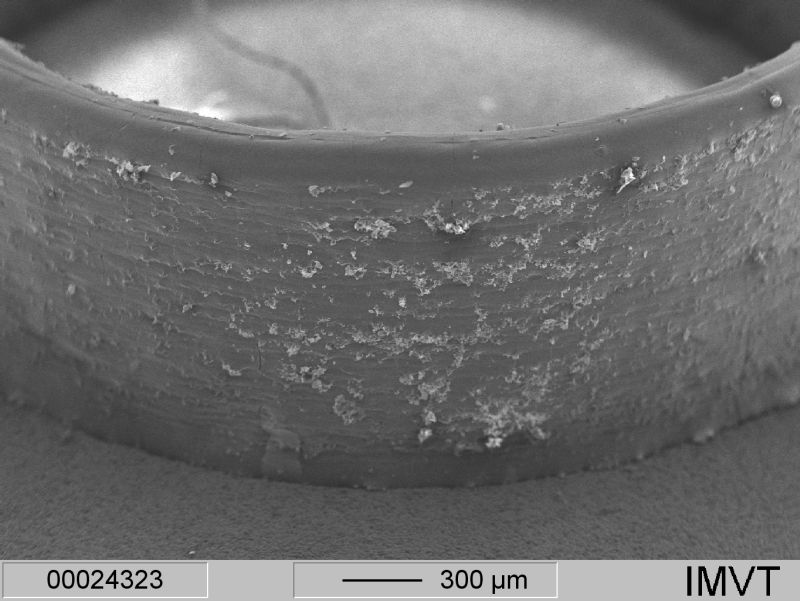
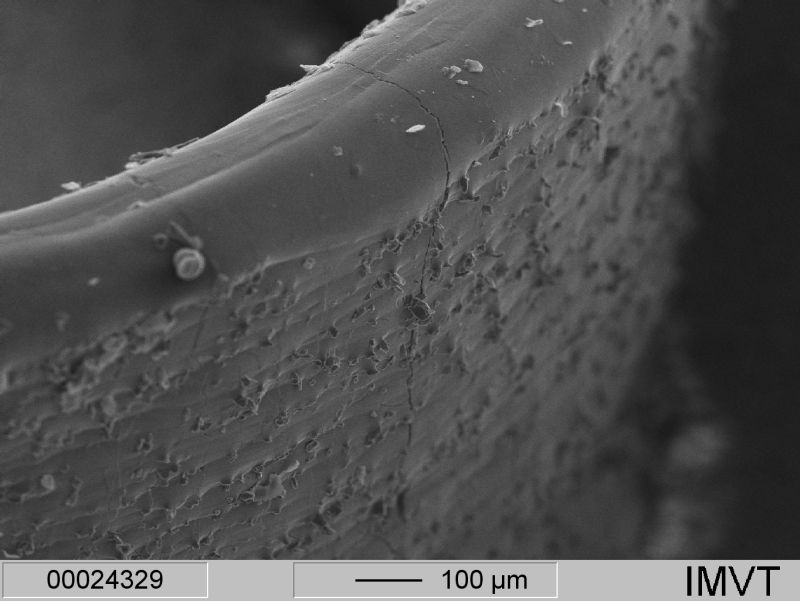
In weiteren Versuchen wurde der Energieeintrag (Energieverteilung) für die einzelnen Belichtungsschritte variiert mit der Zielsetzung rissfreie Wandstrukturen aufzubauen. Abb. 3 zeigt beispielhaft ein Versuchsergebnis mit 6 parallel aufgebauten Wänden. Diese Wandstrukturen haben eine Länge von 3 mm, eine Breite von 0,3 mm und eine Höhe von 0,6 mm in 20 Schichten mit 0,030 mm Höhe je Schicht.
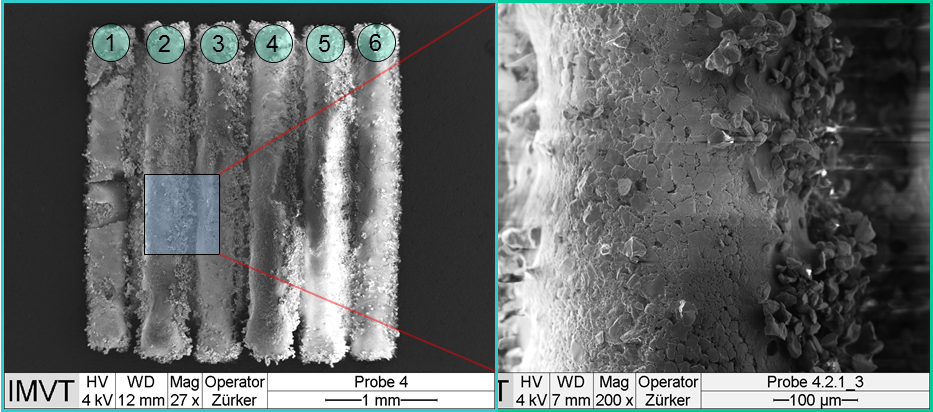
In den beiden äußern Wänden Nr. 1 und Nr. 6 sind Defekte und Risse zu finden. Auf der obersten Schmelzschicht der mittleren vier Wände ist kein Riss zu finden.
REM Aufnahmen der Oberfläche zeigen das erstarrte Gefüge der Schmelzraupen.
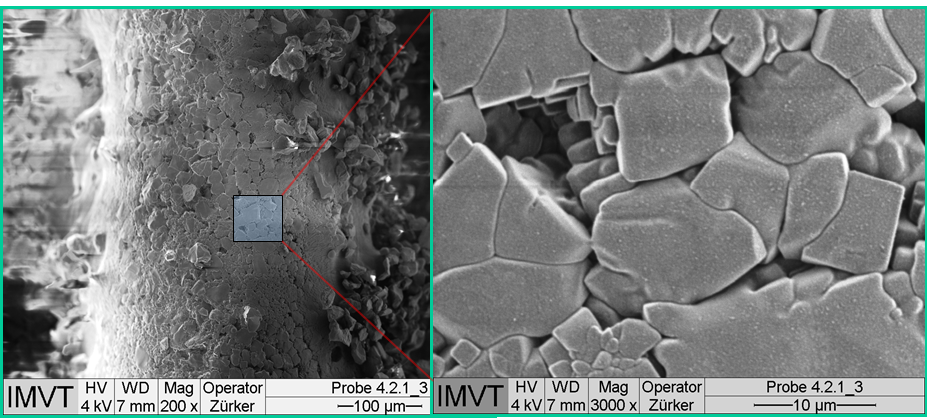
Abb. 4 (Pos. 1) zeigt ein eher grobkörniges Gefüge mit Poren. Der Aufschmelzgrad der Pulverkörner war offensichtlich nicht ausreichend um eine porenfreie Pulververdichtung zu realisieren.
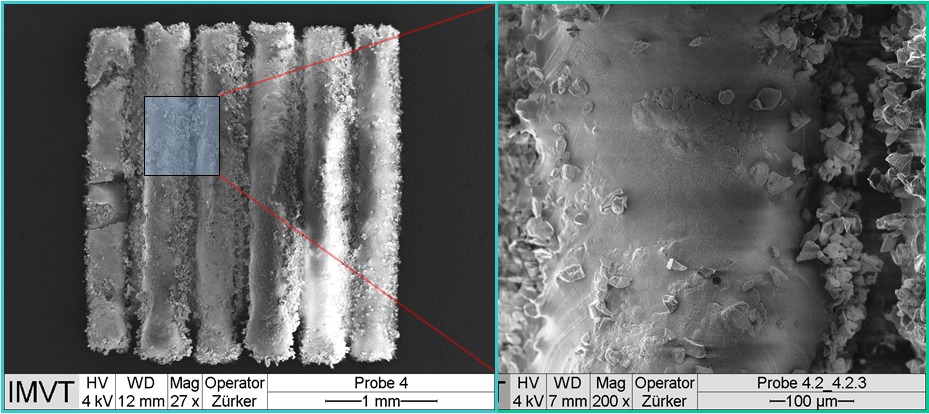
Abb. 5 (Pos. 2) zeigt eine sehr glatte Oberfläche der erstarrten Schmelzraupe mit einem feinkörnigen Gefüge (Abb. 6) Der Aufschmelzgrad der Pulverkörner war ausreichend.
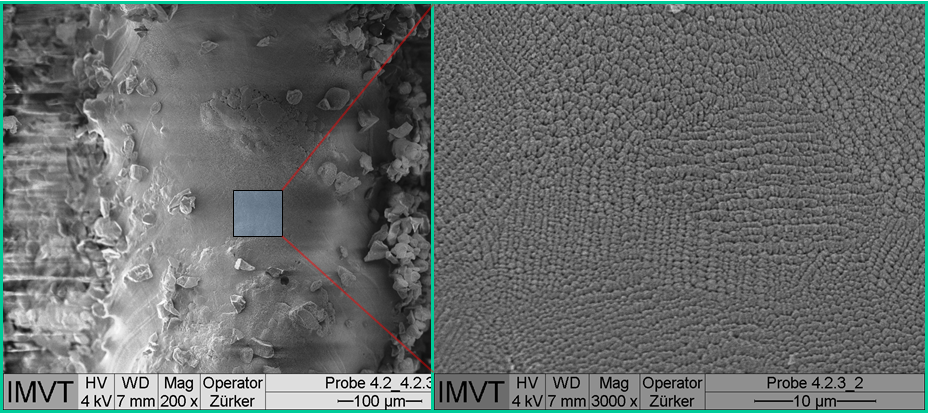
Die Versuchsergebnisse bestätigen, dass man rissfreie mindestens 6 mm lange Schmelzraupen aus einer Keramikpulverschicht aufschmelzen kann.
Bei allen Versuchen mit Keramikpulver am IMVT wurde beobachtet, dass Risse in einer Schmelzraupe nicht durch die nachfolgende Schicht gestoppt werden. Ein Riss pflanzt sich von Schicht zu Schicht bis zur obersten Schicht fort. Diese Beobachtung begründet die Vermutung, dass bei fehlerfreier Oberfläche der letzten Schicht auch die Schichten unterhalb rissfrei sind.
Betrachtet man das Gefüge der Schmelzraupe in Abb. 4 und Abb. 6 eröffnet sich eine weitere Option der Belichtungsstrategie: Der Verdichtungsgrad des Pulvers kann durch den Energieeintrag beeinflusst werden.
Mit dieser Option könnte ein Volumenkörper mit einer definierten Porosität hergestellt werden, zum Beispiel als Filterelement.
Die Versuche zur Entwicklung der Mehrfachbelichtungsstrategie wurden überwiegend mit dem Keramikpulver Al2O3/TiO2 (97/3) durchgeführt. Eine spezielle Parameteroptimierung für diese Keramik ist also nicht auszuschließen. Zur Kontrolle wurden weitere Keramikpulver eingesetzt. Nachfolgend ein Versuchsergebnis mit einer ZrO2 Keramik. Bei diesem Versuch wurde auf einen Metallträger eine 10 bis 20 µm dicke Keramikschicht aufgeschmolzen.
Keramikpulver:
ZrO2/CaO 95/5 (IKH 11201 / Hersteller: Industriekeramik Hochrhein GmbH)
Pulverzusammensetzung: 95% ZrO2 + 5% CaO
Pulverkörnung: -25 +5 µm
Metallträgerplatte:
SIKA-R (Hersteller: GKN Sinter Metals)
Werkstoff: 1.4404 (X2CrNiMo 17-12-2)
Die Trägerplatte wird industriell als metallische Membran hergestellt. Abb. 7 zeigt die Oberfläche der Trägerplatte. Auf diesem Träger wurde eine 30 µm dicke Keramikpulverschicht aufgetragen.
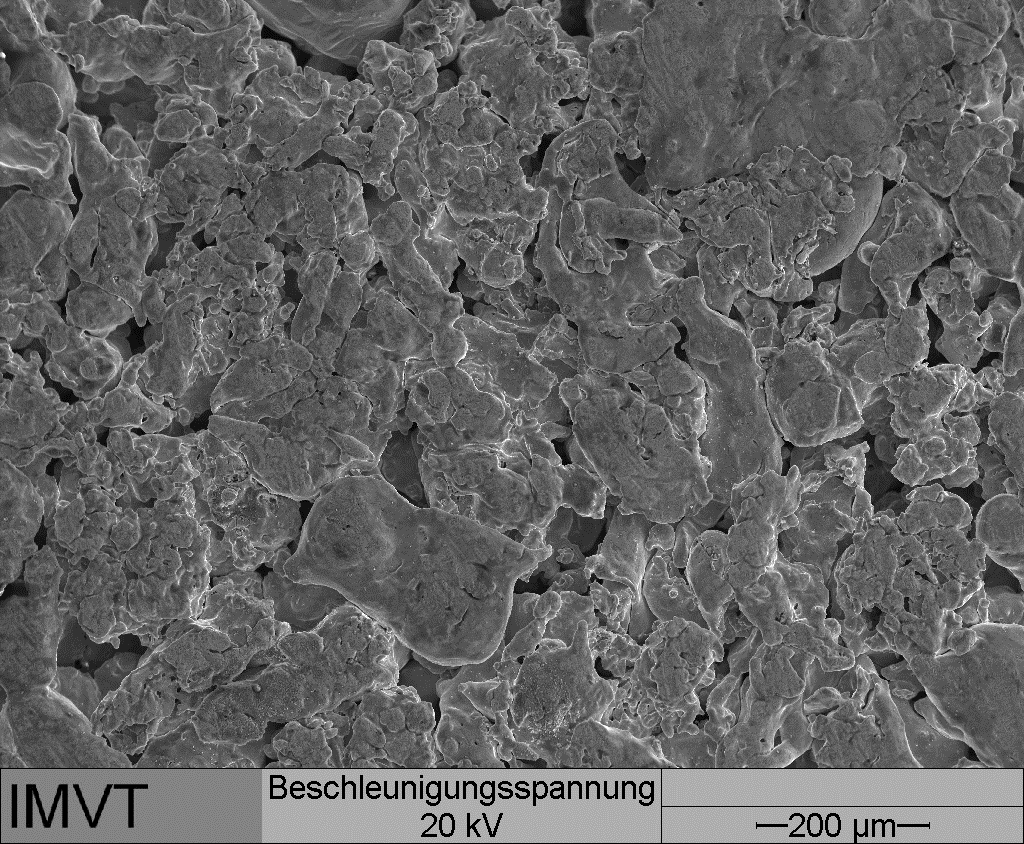
Die Versuche wurden mit einer Vorheiztemperatur von 150 °C durchgeführt. Die Prozessparameter sind vergleichbar mit den optimierten Parametern für die Al2O3/TiO2 Keramik. Mit den gewählten Prozessparametern konnte das ZrO2/CaO Keramikpulver sicher aufgeschmolzen werden. Abb. 8 zeigt die erstarrte Schmelze. Die REM Aufnahme zeigt lokale Rissfelder, aber auch größere Bereiche ohne erkennbare Risse.
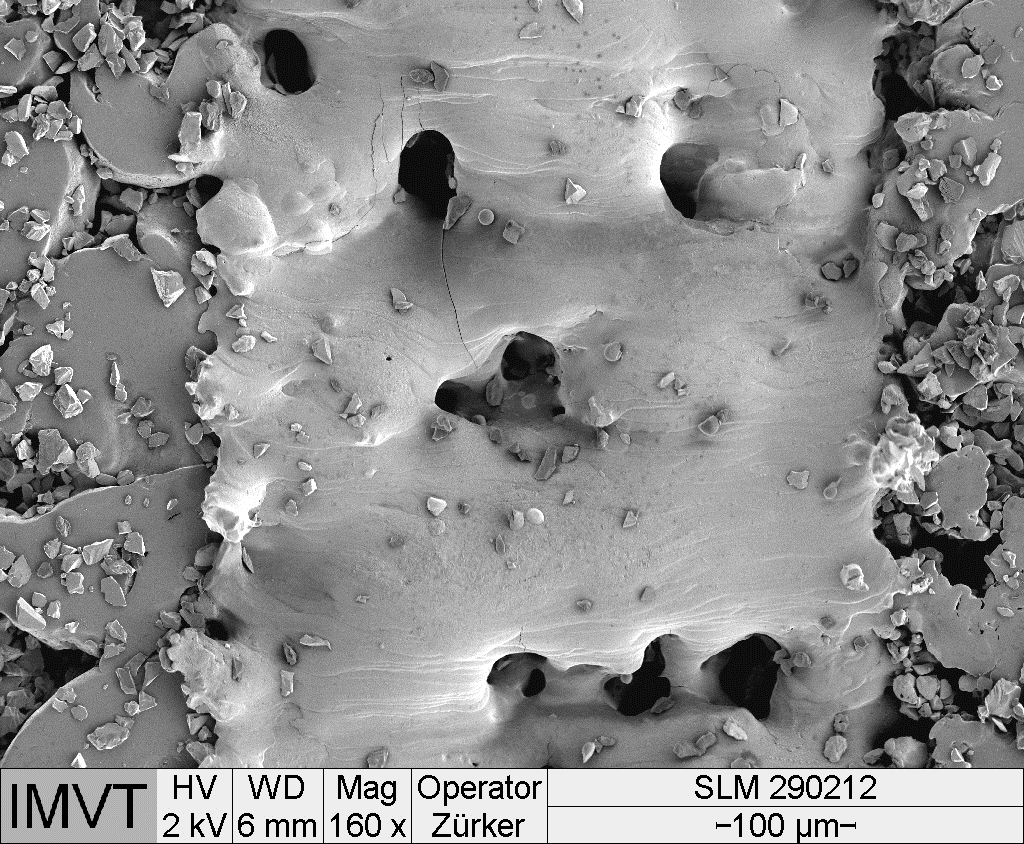
Abb. 9 zeigt ein Versuchsergebnis mit reduziertem Energieeintrag und einer etwa 20 µm hohen Pulverschicht. Die Anzahl der Risse ist deutlich erkennbar reduziert (Abb. 10).
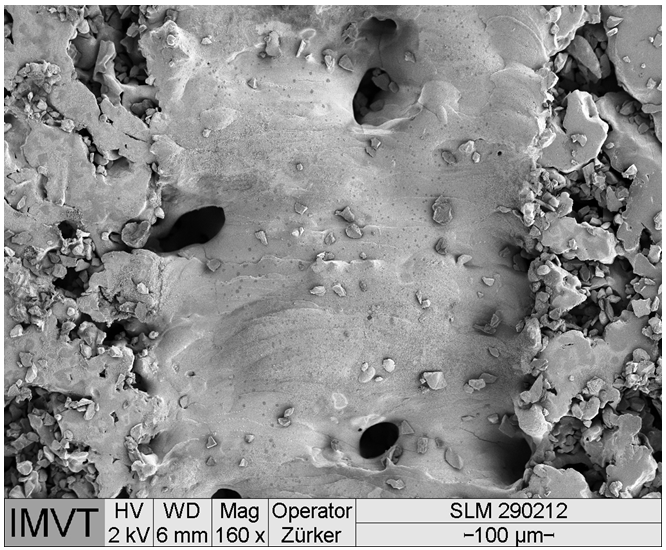
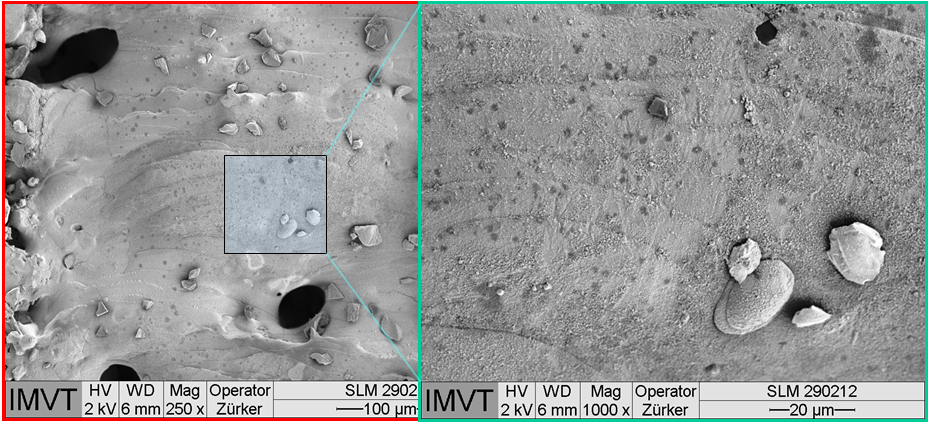
Die Versuchsergebnisse belegen, dass auch eine ZrO2 Keramik sicher und definiert mit der Mehrfachbelichtungsstrategie aufzuschmelzen ist.
Erwähnenswert ist noch die extrem hohe Temperaturdifferenz von mehr als 1000 K zwischen der Schmelztemperatur des Metallträgers (~1500 °C) und der ZrO2/CaO Schmelze (> 2600 °C).
Zusammenfassend kann man feststellen:
Der orts- und zeitabhängige Energieeintrag im Bereich Pulver-Schmelze ist der dominierende Parameter um auch Keramikpulver im SLM-Verfahren einzusetzen.
Durch die Versuche am IMVT wurde die Wissensbasis bezüglich des Aufschmelzvorgangs erweitert und das Prozessmodell weiterentwickelt.
[1] Verband der Keramischen Industrie e.V.: Brevier Technische Keramik.